
Funded: Connemara Discovery Point On Wild Atlantic Way
Minister for Transport, Tourism and Sport, Pascal Donohoe, TD, recently announced €990K for a new Connemara Discovery Point on Wild Atlantic Way, the design of which was produced by Denis Byrne Architects with Sherwood Associates and Cleary and Connolly.
Stories of Marconi Wireless Station and of the first air crossing of the Atlantic by Alcock & Brown will be brought to life to attract visitors. The project at Derrygimlagh, Connemara, Co, Galway is one of the key 15 Signature Discovery Points along the route of the Wild Atlantic Way.
The money, allocated from Fáilte Ireland’s Wild Atlantic Way capital programme, will significantly enhance the site which was the setting for two outstanding technological achievements of the 20th century: the Marconi Wireless Station, the world’s first commercial transatlantic wireless station in 1907; and twelve years later (in 1919) when Alcock and Brown landed on the site marking the first nonstop, trans-Atlantic flight.
Minister Donohoe said: “History was made not once but twice at this rugged outpost overlooking the Atlantic Ocean, yet, today, you would hardly know it. This investment will allow us to bring that history to life and turn what is currently a curiosity into a ‘must-visit’ destination along Ireland’s newest attraction, the Wild Atlantic Way.Our new touring route is already proving popular at home and overseas but, if it is to deliver the increased visitors and revenue we want, we need to bring the local stories alive. Today’s funding marks another chapter in that work.”
The proposed improvements to the Derrygimlagh Discovery Point include a purpose built car and coach park facility with a significant sculpture to celebrate the world’s first transatlantic flight in the car park. Other developments will include a picnic area and a looped walk on existing bog road with six key stops providing opportunities for visitors to engage first hand with the stories of the site including the unique landscape and flora and fauna.
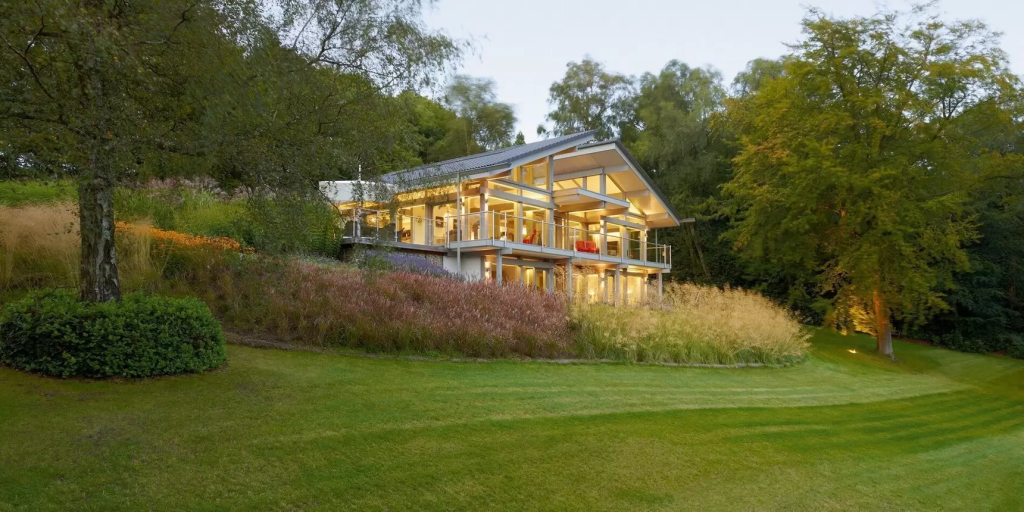
Connecting with Nature – A House in a Garden
The contemporary two-storey Huf Haus is reached via the quiet cul-de-sac road, Abington. Compared to some of its larger neighbours, the 4-bedroomed house is relatively compact at 322 sqm (3,466 sq feet) for reasons of energy efficiency and sustainability. The home was designed primarily “as a house within a garden and to provide, as much as possible, an openness to the landscape”. At ground level, where the living rooms are situated, the house is quite transparent and, as the landscaping develops, will be surrounded by mature trees and hedges.
At first floor level, the bedrooms enjoy sunlight and views to the garden, while the solid gable walls protect the privacy of neighbours. In addition, external blinds with horizontally arranged and movable slats guarantee further privacy and flexible sun protection that can be adapted to every season and time of day. The outer shutters offer visual and glare protection, but above all sun protection. With their outstanding light control and regulation properties, the outer shutters enhance the overall architectural appearance, in which light constitutes an ever-changing, living design element The main structural material is a painted timber post and beam frame, with glass and solid wall infill. A white render finish in all solid walls, with a visible painted timber structure, gives this house its elegant modernist appearance.
Generous and Well-Organised Space
Living spaces in this contemporary home have been efficiently organised to maximise light and a connection with the garden. On the ground floor, the living/dining room and kitchen are open to the landscape. The house also features the now all-important home office. Good storage and a separate utility room will enhance well-being by keeping the interior spacious and clutter-free. The first floor provides four good-sized bedrooms, each with a private bathroom and a balcony overlooking the dining room below.
Adding to the overall sense of space is the generous floor-to-ceiling height. On the ground floor, this varies from 2.65m (8.7 feet) to a lofty 5.61m (18.4 feet) for the double-height space in the dining area, to take advantage of light and views. At first floor level, it is 2.65m throughout, well above the standard floor-to-ceiling height of Irish homes.
Energy Efficiency as Standard
The house has been designed to the highest thermal efficiency standards. The roof and solid walls are very well insulated and triple glazing is employed throughout. An air-to-water heat pump connects to an under-floor space-heating system in a low-energy high-efficiency design. While the house awaits its BER rating, similar Huf houses in Germany and the UK have achieved more than the equivalence of the Irish BER A rating. Every HUF house that leaves the factory has been awarded the highest grade of gold from the German Sustainable Building Council – Europe’s biggest network for sustainable building.
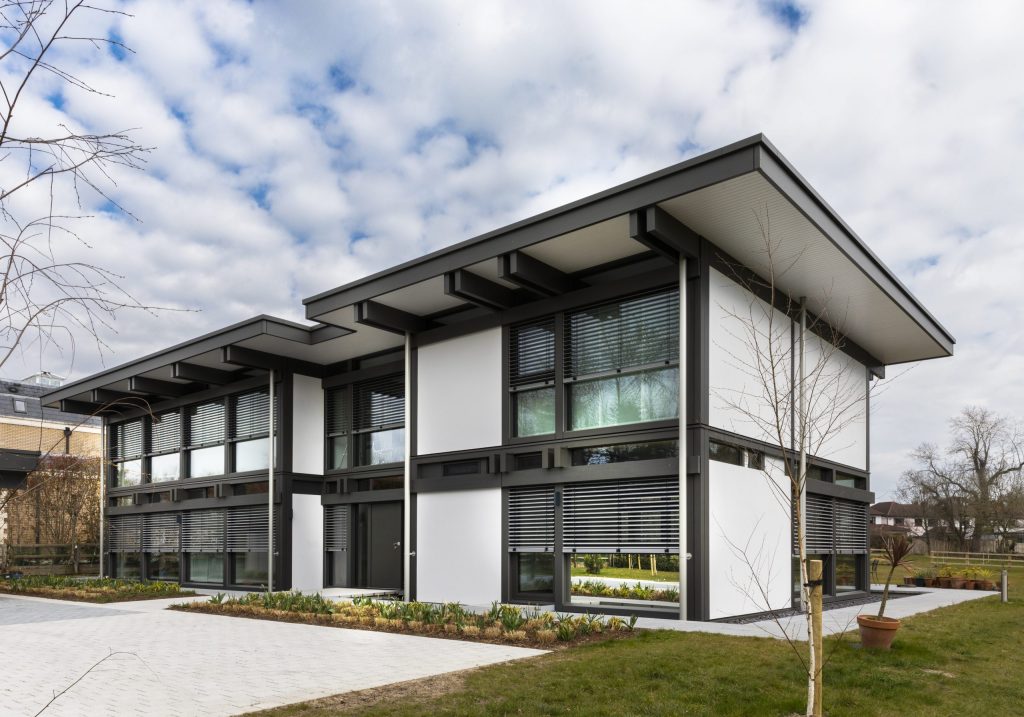
The Huf Haus Design Process in 6 Steps
- The house is designed by Denis Byrne Architects in consultation with the client, initial designs are submitted to the local authority for a pre-planning consultation after which the final design is agreed upon.
- The cost of the house is calculated and a ‘sales contract’ is signed with Huf. DBA Architects then submit the planning application drawings and documents to the local authority.
- The client visits the Huf Haus factory & showhouse complex in Hartenfels to choose every detail of the interior fixtures and fittings and a ‘fit-out protocol’ is completed, agreed and signed. This protocol is incorporated into the working drawing phase and all the elements are brought together, (structure, heating, sanitary, electrical) and a production plan is produced.
- Materials are ordered and production takes place. Work in the factory normally takes in the region of 12 weeks, usually during this time the site is also being prepared. Once the house is ready, it is put on lorries and driven to Ireland.
- The on-site construction stage is radically different from the traditional Irish build; the house that has been made in the factory in Hartenfels is now completed on-site by the German construction team. The building of the exterior structure of the house on the site takes one to three weeks (depending on size) and once complete the interior works starts, again depending on the size of the project this takes between twelve and twenty weeks.
- The ‘Feel Good’ factor – HUF HAUS’ service and support do not end with the handover. Their after-care specialist ServiceART provides a speedy, flexible and reliable service as part of the home’s warranty should any work or service be required after handover. HUF HAUS and Service ART are also delighted to assist owners beyond the warranty period – a life-long partner for you and your home.
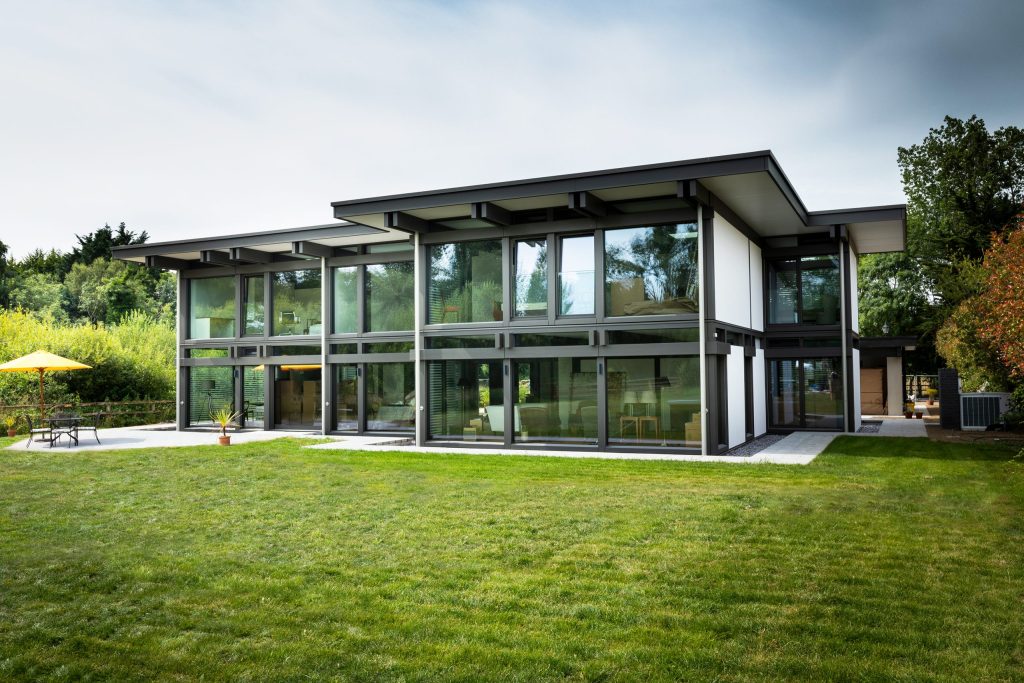
Huf Haus produce ‘turn-key houses, which means that the underfloor heating system – a sustainable air-to-water heat pump, electrical installations, floor coverings – indeed everything above ground level – is included in the fixed price, as is VAT, delivery, architect’s fees and the German construction crew. Exclusions are groundworks and site preparation including drainage as well as landscaping. The kitchen is also excluded as there are many options, but high-spec bathrooms are included.